Development of a Handcycle using DuraForm® Polyamide Plastic
Craig Markovitz1,3 ; Joseph Olson, BSE2,3 ; Jeremy Puhlman, BSE3
1 Department of Biomedical Engineering, Washington University in St. Louis;
2 Department of Rehabilitation Science and Technology, University of Pittsburgh;
3 Human Engineering Research Laboratories, VA Healthcare System, Pittsburgh, Pennsylvania
ABSTRACT
A fourth generation, delta-style handcycle was developed for eventual use by veterans at Walter Reed Medical Center. Since a computer model can only show a limited amount of information, a mocked-up version using aluminum and DuraForm® polyamide (PA) plastic was fabricated to test the overall geometric properties of the design while also allowing us to analyze rider comfort. The polyamide plastic has the key advantages of decreased fabrication time and cost, making it an effective material to be used in an initial prototype. However, the material’s disadvantages include its relative weakness when compared to other common materials such as aluminum and carbon fiber and the outer layer’s tendency to deteriorate. Overall, the mocked-up version made of aluminum and the DuraForm® polyamide (PA) plastic was successful in providing a tangible prototype that was fast and inexpensive to create.
KEYWORDS
handcycle; selective laser sintering; DuraForm® polyamide plastic; mocked-up; helicoil
BACKGROUND
Handcycling is a popular activity for people with lower limb impairments. In both its racing and recreational forms, handcycling allows individuals with many different disabilities to remain physically active. Early handcycles had large, upright designs, making them difficult to maneuver, transport, and store (1). However, modern day handcycles have evolved into efficient, lightweight models, giving rise to the sport’s inclusion in the International Paralympic Committee (IPC) cycling program in 1998 and more recently into the Paralympic Games in 2004 (1).
Three previous generation handcycles have been designed at the Human Engineering Research Laboratories (HERL), the first being designed for use in India, the second for the United States, and the third was never physically built (2,3,4). Similar to the overall market, the first generation design was large and upright while the newer generations switched to the sleeker recumbent-style. The fourth generation design features the overall structure of the third generation prototype while incorporating more simplified front and rear clamps for ease of machining.
METHODS
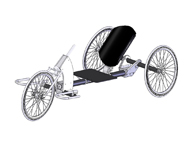
The design for the fourth generation handcycle was produced using SolidWorks, which produces a 3D model that can be rotated and viewed from all angles. While this produces a clear image of the entire handcycle, important factors such as rider comfort and geometric stability cannot be easily analyzed using only this computed model.
Since computer models are so limiting, it is often advantageous to produce a mocked-up version of complex designs in order to get a clear visual of the prototype and make any necessary changes to the design before the final product is created. Before the final prototype of the fourth generation handcycle is produced using expensive carbon fiber tubing and aluminum clamps, a mocked-up version using inexpensive materials was created. The mocked-up prototype features light aluminum framing and Duraform® polyamide plastic clamps machined using Selective Laser Sintering (SLS). SLS is a process that produces parts directly from 3D CAD models, preventing the need for manual tooling. The machine forms the part using a laser that fuses DuraForm® polyamide powder layer by layer into the desired shape (5). The SLS process can finish a part in several hours that would otherwise take days or weeks to manually machine, while simultaneously allowing the machinist to focus on other tasks while the parts are being created. The polyamide plastic allows for quick machining of difficult parts, such as the front and rear clamps, while the aluminum adds functionality to the prototype by allowing a rider to sit in the handcycle without causing failures in the framing. The plastic clamps are attached to the frame by being pushed down around the aluminum tubing with epoxy and held in place by screws attached to helicoiled holes.
RESULTS
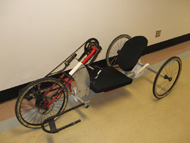
The results of the mocked-up prototype show a relatively stable geometry, meaning no major adjustments in the model need to be made.
The entire prototype was built quickly mostly due to the fact that the polyamide plastic pieces can be produced overnight. The most difficult piece of the handcycle to machine was the side plate of the front clamp, which needed to be made out of aluminum in order to prevent failure of the frame with the rider’s weight added. The same piece that took only twelve hours overnight in the SLS to get an idea of its size and shape took a full day and two machinists to build out of aluminum using both a manual mill and a Computer Numerical Controlled (CNC) mill.
While the polyamide plastic greatly improved scheduling and budgetary factors, it also caused several problems. One minor dilemma occurred when screwing the front clamp pieces together into helicoiled holes. Since the polyamide plastic required helicoiling for screws to remain fixed in the material, holes cannot be designed close to the outer edges of the piece. In the outer wall of the front clamp, several holes were designed too closely to the edge, causing the helicoils to break through the material. To remedy this problem, the clamps were redesigned and fabricated with an additional two millimeters on each side, preventing this failure from occurring.
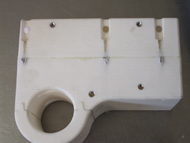
Another failure occurred where the front clamp was attached by epoxy to the main frame tube. When manually testing the fork steering, the front clamp became loose from the main frame tube and could freely rotate, causing the clamp, fork, and footrests to be slanted. There are three possible explanations that can explain the failure. The first explanation is that the Duraform® clamp was not cleaned properly after being machined, leaving leftover, non-compacted material on the outside of the clamp and subsequently causing it to become loose in the tube. Another possible explanation is that since the Duraform® material can easily flake off, the epoxy could have no longer been attached to the clamp due to the outer layer of plastic becoming loose. The final possible explanation is that when hammering the steering compensatory plug into the front of the main frame tube, the shock forces could have caused the epoxy to lose its hold. All three of these explanations for the failure represent downfalls of using the Duraform® polyamide plastic, since pieces must be thoroughly cleaned after production, the outer layer of the pieces can easily crumble off, and the material is not as strong as many other common handcycle materials, such as aluminum or carbon fiber.
CONCLUSION
Having a tangible prototype is much preferred over a simple computer model since it allows for the analyzing of factors such as rider comfort and geometric stability. It also provides a convenient opportunity to test other design ideas, such as negative camber wheels and different steering compensatory plugs. Additionally, a concrete model gives the designers a new way to look at the blueprint while actually building it piece by piece, possibly leading to new innovative designs.
The greatest advantage of using the Duraform® polyamide plastic was the amount of time and work saved in fabrication. The extra time spent helicoiling the holes in the polyamide clamps and redesigning and fabricating the new clamps when the holes were found to be too close to the edge was miniscule in comparison to the time saved by using SLS on the pieces in lieu of machining them by hand out of another material. New parts could easily and quickly be remade while work was being done on design aspects of the handcycle or even overnight. The greatest disadvantage of using the Duraform® polyamide plastic was its relative weakness. Since one of the goals of the initial prototype required that a rider sit in the handcycle, certain parts of the handcycle such as the clamp plating could not be made out of the plastic but had to be machined out of aluminum. Overall, however, the few failures and downfalls of the Duraform® polyamide plastic experienced during production of the initial prototype of the fourth generation handcycle did not take away from the huge time, work, and cost advantages of using the material.
REFERENCES
- “Handcycling History.” Wheelchair Sports Victoria. 2007. 17 July 2007. <http://www.wsv.org.au/sports/hand_cycling/handcycling_history.html>.
- Cooper, R. A. & Cooper, R. (2003). Design of an arm-powered general purpose tricycle for use by people with mobility impairments. Saudi Journal of Disability and Rehabilitation 9[2], 92-96.
- Zipfel E, Cooper RA, Chavez E, Duncan J, McCartney M, Ammer B et al. (2003). HAND CYCLE: A DESIGN EVALUATION. Accepted for presentation 26th Annual RESNA Conference. Atlanta, Georgia.
- “Design and Development of a Carbon Fiber Handcycle.” Joe Olson BS, Rory Cooper PHD, Megan Langdon, Jeremy Puhlman BS, Mark McCartney.
- “How SLS (Selective Laser Sintering) process works.” Arptech. 1 August 2007. http://www.arptech.com.au/slshelp.htm.
ACKNOWLEDGEMENTS
The funding for this research was provided in part by the National Science Foundation, Project EEC 0552351
CONTACT INFORMATION
Craig Markovitz
192 Meadowfield Lane
Jefferson Hills, PA 15025
Phone: (412) 965-5132
Email: cdm3@cec.wustl.edu